Fundamentals of Motor Control Design
Time:2023-08-24
Views:737
Both software and hardware are part of all motor control systems, such as IGBT, WBG semiconductor, and MCU. The development of Industry 4.0 strongly relies on motor control, but energy consumption is a key issue as it is rapidly growing and demand increases with the complexity of design, as many electronic technologies have strict control requirements. Broadband gap (WBG) materials are an example of this situation.
From a functional perspective, motor control consists of several levels. For example, motion control requires the execution of very complex and computationally intensive control algorithms. Motor control covers a wide range of applications, from simple control of fans and pumps to more complex industrial control problems, including robots and servo mechanisms. Here, let‘s take a look at the key components of the motor control system.
Electric motors and drives are common because they are cheaper and consist of a stator (fixed part) (i.e. permanent magnet) and a moving part (rotor), which accommodates the winding connected to the commutator providing current. The speed control of the motor is achieved by adjusting the DC current. For this purpose, according to the nature of the application, a full bridge, half bridge, or step-down converter is used to drive the DC motor.
AC motors are basically composed of transformers, with the primary part of the transformer connected to AC voltage and the secondary part conducting induced secondary current. Microprocessor based electronic devices, inverters, and signal conditioning are used to control the speed of the motor.
A controller is an electronic device that acts as the "brain" in a control system. The number of controllers used varies depending on the number of individual processes that need to be controlled. For a complex system, there may be many controllers. Each controller can send commands to the motor and receive commands from the actuator itself.
The robot systems used in industrial applications mainly use three-phase motors powered by alternating current (AC). As an example, Figure 1 shows a block diagram of an electronic control circuit where a dedicated microcontroller (MCU) generates a PWM signal. As an alternative to MCU, DSP or FPGA solutions are more suitable for implementing complex digital filtering algorithms.
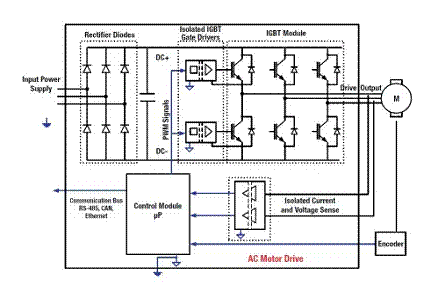
Figure 1: Control Block Diagram of AC Powered Three Phase Induction Motor: Control Block Diagram of AC Powered Three Phase Induction Motor (Texas Instruments). The controller example for a DC motor is Trinamic‘s TMCM-1637 5-A RMS and TMCM-1638 7-A RMS slot type modules, with two field oriented controllers/drivers and Hall and ABN encoder functions added for field oriented control (or vector control). These modules support single-phase DC motors, two-phase bipolar stepper motors, and three-phase brushless DC (BLDC) motors (Figure 2).
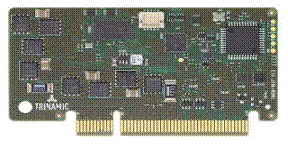
TMCM-163x Solution Figure 2: TMCM-163x Solution (Trinamic) IGBT Insulated Gate Bipolar Transistor (IGBT) embodies true innovation in the field of power control electronics. As a switching solution, innovation comes from high switching frequencies. IGBT represents the basic functions of power control equipment and is very suitable for solving complex motor control problems.
The solution establishes a good relationship between switching speed and behavioral stability under particularly extreme usage conditions, such as when implementing inverters to drive electric motors in the automotive industry. STMicroElectronics‘ 1200V IGBT S series is an example. These IGBTs have been optimized for low frequency (up to 8 kHz) usage and have the characteristic of low V ce (sat). The 1200V IGBT S series is based on third-generation trench gate field cutoff technology.
However, broadband gap materials, gallium nitride, and silicon carbide are making progress in the field of motor control applications as substitutes for silicon based devices. In the field of power electronics, the main advantages of WBG materials include lower power loss, higher efficiency, higher switching frequency, more compact size, higher operating temperature (far exceeding the upper limit of 150 ° C achievable by silicon), higher reliability under difficult working conditions, and high breakdown voltage.
For example, GaN high electron mobility transistors (HEMTs) have higher electron mobility, which can be converted into higher switching speeds because the charges typically accumulated in the junction can be dispersed more quickly. GaN can achieve faster rise time, lower drain source conduction resistance (RDS (on) value, and lower gate and output capacitance, all of which contribute to its ability to achieve low switching losses and operate at up to 10 times the switching frequency compared to silicon.
Reducing power loss brings additional benefits, such as more efficient power distribution, less heat dissipation, and simpler cooling systems. Many motor control applications require fans to provide forced air cooling in order to operate within the safe operating limits of the equipment. By using GaN, power consumption can be reduced and "fan free" operation can be achieved, which is particularly important for lightweight applications such as electronic drones.
In industrial power supply applications, electronic designers can also benefit from using SiC MOSFETs, which significantly improve efficiency, reduce heat sink size, and reduce costs compared to traditional silicon based solutions such as IGBT. SiC technology can achieve extremely low RDS (on) per unit area, high switching frequency, and negligible energy loss during the reverse recovery phase after the body diode is turned off.
The use of SiC devices in motor control and power control applications is a real breakthrough, as it has the characteristics of energy conservation, reduced size, higher integration, and high reliability. These functions make it very suitable for high reliability fields such as automotive and industrial automation control.
In industrial drives, special attention must be paid to the speed of opening and closing the shuttle. In fact, SiC MOSFET dV/dt can reach a much higher level than IGBT. If not handled properly, high commutation dV/dt can increase voltage spikes on long motor cables and may generate common mode and differential mode parasitic currents, which can lead to winding insulation and motor bearing failures over time. Although faster opening/closing can improve efficiency, for reliability reasons, the typical dV/dt in industrial drives is usually set at 5 to 10 V/ns.
The comparison of two similar 1.2kV power transistors (SiC MOSFET and Si based IGBT) by Italian semiconductor proves that even under the application condition of 5 V/ns, compared with Si IGBT (Figure 3).
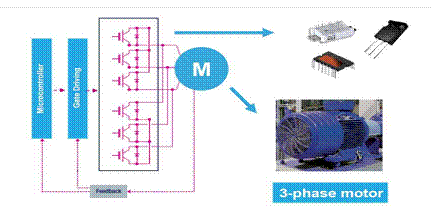
Figure 3: The use of silicon carbide devices in motor control and power control applications is generally a real breakthrough due to the characteristics of energy-saving, size reduction, integration opportunities, and reliability of STMicroElectronics based on two-level and three-phase inverters. Among other options, switching frequency can now be used in the inverter circuit of the connected motor, which brings important advantages to motor design. For example, Infineon Technologies‘ CoolSiC MOSFET based on SiC adopts. XT interconnection technology and 1200V optimized D? PAK-7 SMD packaging can achieve passive cooling in power density critical motor drive fields such as servo drives, providing support for the robot and automation industries to implement maintenance free and fan free motor inverters (Figure 4).
In the field of automation, fanless solutions bring new design opportunities as they save maintenance and material costs and effort. For example, Infineon‘s CoolSiC groove MOSFET chip solution using. XT interconnect technology provides attractive heat dissipation capabilities in a small size, making it very suitable for driving integration in robotic arms. The short-circuit withstand time of CoolSiC MOSFET SMD devices is 3? s. The rated resistance is between 30 m Ω and 350 m Ω. This meets the requirements of the servo motor.
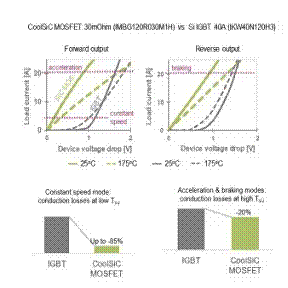
The conduction loss reduction in all operating modes is shown in Figure 4: The conduction loss reduction in all operating modes (Infineon Technology) microcontroller motor control solution consists of hardware and software components. Hardware components are electronic control devices such as IGBT, SiC and GaN MOSFETs, power diodes, etc., while software components solve increasingly complex and precise hardware control problems. The emergence of optimized computing architectures for the control and management of power devices has enabled developers to achieve performance that cannot be achieved in the control field.
Enzipu Semiconductor and Renesa Electronics are just a few examples. NXP‘s MPC57xx series 32-bit processor is based on Power Architecture technology and is suitable for automotive and industrial powertrain applications in addition to other automotive control and function management functions. This processor provides AEC-Q100 quality, on chip security encryption protection for tamper resistance, and supports ASIL-D and SIL-1 functional security (ISO 26262/IEC 61508). They provide Ethernet (FEC), dual channel FlexRay, and multiple 6 SCI/8 DSPI/2 I 2C for different communication protocols.
Renesas provides a RA6T1 32-bit MCU based on the Arm Cortex-M4 core, operating at a frequency of 120 MHz, and features a series of peripherals optimized for high-performance and precision motor control. A single RA6T1 MCU can control two BLDC motors simultaneously. In addition, the Google TensorFlow Lite Micro framework for TinyML applications has added enhanced fault detection capabilities to the RA6T1 MCU, providing customers with intelligent, easy-to-use, and cost-effective sensorless motor systems for predictive maintenance.
The motor requirements vary depending on the application and may need to be tailored to specific requirements?? Use case optimization and fine-tuning. The market provides a variety of IGBT, WBG semiconductor, and MCU solutions to meet these requirements. However, new hardware needs to be developed to offload real-time critical tasks from processors, while supporting more diagnostic, predictive maintenance, artificial intelligence, and functional safety systems.
Disclaimer: This article is transferred from other platforms and does not represent the views and positions of this site. If there is any infringement or objection, please contact us to delete it. thank you! |