Detailed elements of PCB inspection
Time:2023-02-02
Views:1340
When the layout and wiring of a PCB is completed, and the connectivity and spacing are checked without error, is a PCB completed? The answer, of course, is no. Many beginners, including some experienced engineers, tend to rush through the process and neglect the later inspection due to time constraints, impatience or overconfidence. As a result, some very basic BUGs appeared, such as the line width was not enough, the component label screen was pressed on the vias, the socket was too close, and the signal appeared a loop. This will lead to electrical problems or process problems. In serious cases, it is necessary to re-plate and cause waste. Therefore, after the layout and wiring of a PCB is completed, a very important step is post-inspection.
There are many detailed elements in PCB inspection. I have listed some of the most basic and error-prone elements for later inspection.
1. Component packaging
(1) Pad spacing. If it is a new component, you should draw the component package by yourself to ensure the proper spacing. The pad spacing directly affects the component welding.
(2) Through hole size (if any). For plug-in devices, enough allowance should be reserved for the size of the via, which is generally not less than 0.2mm.
(3) Contour screen printing. The outline screen printing of the device should be a little larger than the actual size to ensure that the device can be installed smoothly.
2. Layout
(1) IC should not be close to the board edge.
(2) Components of the same module circuit shall be placed close to each other. For example, the decoupling capacitor should be close to the power pin of the IC, and the components that make up the same functional circuit should be placed in a region with clear layers to ensure the realization of functions.
(3) Arrange the position of the socket according to the actual installation. Sockets are led to other modules. According to the actual structure, in order to facilitate installation, the principle of proximity is generally adopted to arrange the location of sockets, and generally close to the board edge.
(4) Pay attention to the direction of the socket. The sockets are all directional. If the direction is reversed, the wire will have to be customized. For the flat socket, the socket direction should be toward the outside of the board.
(5) Keep Out area cannot have components.
(6) The interference source shall be far away from the sensitive circuit. High-speed signal, high-speed clock or high-current switch signal are interference sources, and should be far away from sensitive circuits, such as reset circuit and analog circuit. They can be separated by paving.
3. Wiring
(1) Lineweight size. The line width shall be selected according to the process and current carrying capacity. The minimum line width shall not be less than the minimum line width of the PCB manufacturer. At the same time, ensure the carrying current capacity, and generally select the appropriate line width at 1mm/A.
(2) Differential signal line. For USB, Ethernet and other differential lines, pay attention to the equal length, parallel and plane routing, and the spacing is determined by impedance.
(3) Pay attention to the return path of high-speed line. High-speed lines are prone to generate electromagnetic radiation. If the area formed by the routing path and the return path is too large, a single-turn coil will form to radiate electromagnetic interference outward, as shown in Figure 1. Therefore, when routing, it is necessary to pay attention to the return path nearby, and the multi-layer board is equipped with power supply layer and ground plane to effectively solve this problem.
(4) Pay attention to the analog signal line. The analog signal line should be separated from the digital signal. Try to avoid passing by the interference source (such as clock, DC-DC power supply), and the shorter the line is, the better.
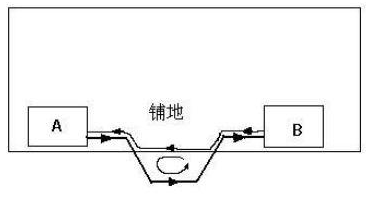
Figure 1
4. EMC and signal integrity
(1) Terminate resistance. It is better to connect a matching resistor at the end of high-speed line or digital signal line with high frequency and long routing.
(2) Input signal line is connected with small capacitance in parallel. The signal line input from the interface should preferably be connected to a small capacitance at the level of Pifa near the interface. The capacitance is determined by the strength and frequency of the signal and cannot be too large, otherwise the signal integrity will be affected. For low-speed input signals, such as key input, 330pF small capacitance can be selected, as shown in Figure 2
(3) Driving ability. For example, the switch signal with large driving current can be driven by triode; A buffer (such as 74LS224) can be added to drive the bus with a large number of fanouts.
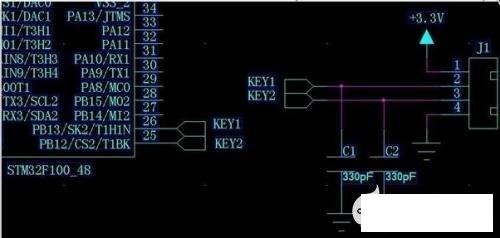
Figure 2
5. Silk screen
(1) Board name, time and PN code.
(2) Dimensions. Mark the pins or key signals of some interfaces (such as array).
(3) Component label. Component labels shall be placed in appropriate positions, and dense component labels can be placed in groups. Be careful not to place it in the hole.
6. Others
Mark point. For PCBs requiring machine welding, two or three Mark points need to be added.
Disclaimer: This article is transferred from other platforms and does not represent the views and positions of this site. If there is any infringement or objection, please contact us to delete it. thank you! |