The evolution of automotive image sensors
Time:2024-05-24
Views:174
Source: ON Mei By Sergey Velichko
It all started 18 years ago when I started working on one of the first automotive CMOS image sensors for rear-view cameras (RVC). At the time, having an RVC to help drivers see behind the car was a great innovation. Two decades later, RVC has become standard in modern vehicles, and more cameras are paving the way for advanced driver assistance systems (ADAS). As Aptina spun off from what was then Micron‘s image sensor division and was later acquired by onsemi, my career changed and the ADAS system went through a series of major changes.
Today, more advanced automotive systems alert drivers when they detect a close object or a car in a blind spot, when they deviate from the lane, and when they maintain speed and distance in cruise mode. Many of these familiar safety features are enabled by car image sensors. It‘s been a very rewarding experience for me personally to be a part of this transportation revolution. I had the opportunity to work on the ON Beauty team and strive to bring many groundbreaking inventions to the industry that are now the norm. For example, we introduced dual-gain pixel technology and high dynamic range imaging (HDR), which are now used in many sensor designs. I am proud to say that most ADAS systems use image sensors developed by On.
Over the course of my career, the development of image sensing technology has changed dramatically. I‘ve seen firsthand the remarkable progress being made in in-car image sensors.
Resolution
Image resolution is one of the important parameters to measure image quality. Especially for vehicle-mounted imaging, higher resolution means sharper edges and finer details. Just imagine, when Video Graphics Array (VGA) sensors were just coming out, they could only produce images of 300,000 pixels (0.3MP, 640 H x 480 V). Our AR0820AT is the first automotive 8.3-megapixel (8.3MP, 3840 H x 2160 V) image sensor on the market. This high resolution allows a single camera to support multiple applications (such as vision and perception) and enable better object detection. As more and more automotive applications require larger amounts of imaging data to help make safety-critical decisions, we can expect the market to continue to grow in the future for higher resolution.
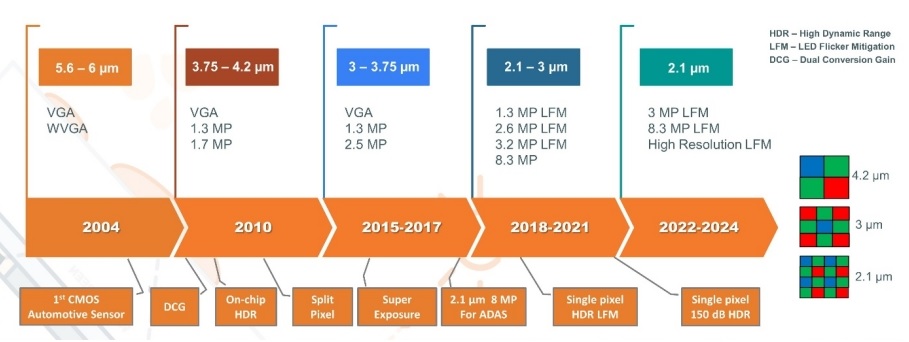
Figure 1. On automotive image sensor development trend
Pixel size
Pixel size is another factor to consider when choosing a sensor, which needs to be perfectly balanced with speed, sensitivity, and image quality. Larger pixels have a larger area to collect usable light, but that doesn‘t always mean better image quality. A sensor with smaller pixels may outperform a sensor with larger pixels when covering the same optical area. Our Hyperlux series is an example of how a 2.1μm pixel sensor outperforms a 3μm pixel sensor in a typical automotive environment: it performs well in low light, total signal-to-noise ratio (SNRs), and HDR. As we develop more advanced image sensors, the pixel size has shrunk from the larger 6μm to our current 2.1μm super-exposure pixel, while improving overall performance.
Exposure HDR technology
We were the first company to invent large and small pixel technology to generate HDR images. By adopting a small pixel approach, the sensor area dedicated to a single pixel is divided into two parts: a larger photodiode covers most of the area, and a smaller photodiode takes advantage of the remainder. However, due to the degradation of image quality, increased dark noise, and decreased performance, especially at higher temperatures, we no longer use this technology.
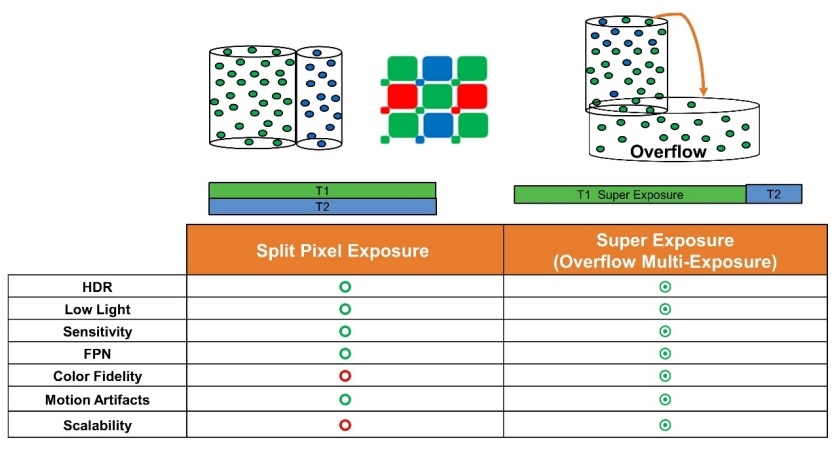
Figure 2. Comparison of exposure techniques
Our solution to these shortcomings is Super exposure technology, also known as overflow multiple exposure technology. The technique adds an area within the pixel to house the part where large signals or charges spill out. This method is like using a bucket to catch rain water, and if the rain overflows the bucket, we have a larger basin to hold the excess water. The signals inside the "bucket" can be read very precisely, so we can achieve excellent low-light performance; The overflowing basin contains all the excess, extending the dynamic range and the ability to capture the true colors of bright objects and scenes. As a result, the entire pixel area can be applied in low light conditions without saturation in bright light conditions. As a result, superexposure technology provides better image quality for HDR scenes in automotive applications, including capturing all the colors and details of flashing LED lights and signs.
Dynamic range
Dynamic range refers to the ratio between the brightest and darkest parts of a scene. Our image sensors were the first to achieve 120dB and then 140dB high dynamic range (HDR). Our Hayabusa series is the industry‘s first commercially available sensor with 120dB HDR and LED Stroboscopic suppression (LFM). Recently, we introduced the Hyperlux family of image sensors with industry-leading 150dB HDR LFM performance and enhanced image quality.
The 8.3-megapixel AR0823AT and 3-megapixel AR0341AT are the first products to feature Hyperlux technology. With superior HDR performance, Hyperlux is able to deliver colorful, sharp, and detail-filled images, which, due to its extremely stable nature and not affected by changes in temperature or light conditions, lay the foundation for a design with higher security. As shown in Figure 3, Hyperlux sensors perform well in the most demanding environments and extreme conditions.
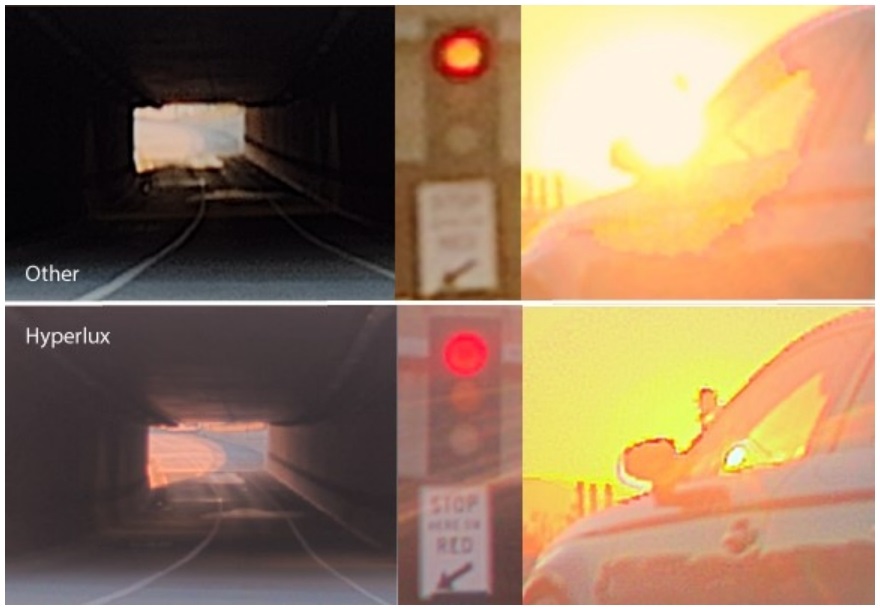
Figure 3. High dynamic range performance comparison between Hyperlux and competing sensors
Car camera systems are a key component in active safety because they are the only way to perceive the color, shape, and size of different objects on the road. Throughout its history, the ON team has consistently worked hard to innovate and set new standards in low-light environments, high dynamic range (HDR), image quality and clarity. This will help vehicle manufacturers (Oems) successfully upgrade early rear-view cameras (RVCS) to Level 2 autonomous vehicle systems and actively implement L2+ and L3 level driving automation. With industry-leading performance and functionality, Hyperlux sensors are expected to improve safety metrics and enable high-speed autonomous driving while reducing system development costs. Therefore, it is not surprising that many Oems and Tier 1 suppliers have chosen to incorporate ON image sensors in their ADAS camera designs.
The road to a safer and better future does not stop there. Together, let us continue to move towards higher levels of road safety and driving automation.
Disclaimer: This article is transferred from other platforms and does not represent the views and positions of this site. If there is any infringement or objection, please contact us to delete it. thank you! |